The electric motor which runs asynchronous speed is known as induction motor and an alternate name of this motor is the asynchronous motor. With the technology most diffused among motors today the asynchronous motor one or Induction Motor IM the improvements demanded in the future will not be possible at least at reasonable costs and for all power rangesThese aspects combined with other factors such as the growing awareness of the importance of decreasing energy consumptions are leading to the adoption of motors scarcely.
Another Way To Make An Energy Efficient Motor Machine Design
Important role of enclosure.
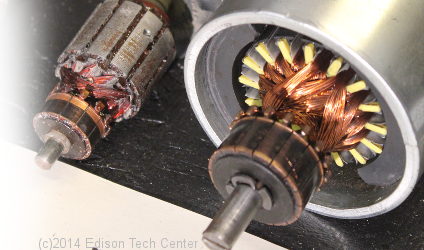
Most efficient electric motor type. A Turntide switched reluctance motor. Claimed to be the worlds most efficient and intelligent Turntide is also setting its sights on other applications including electric vehicles EVs. Where most motors suffer from torque pulsing or cogging at slow speeds which could make an electric car take off in a jerky manner the HET is able to produce overlapping power pulses around.
2 Toshiba a world-leading diversified manufacturer and solutions provider entered the electric motors industry in 1970 and has since become known for manufacturing some of the most reliable robust electric motors in the global marketThe company offers a wide range of low- and medium-voltage motors that are setting new standards in extreme duty performance and durability. BLDC motors are suitable for high power density design approach. This is really informative and handy when you need to choose a type of electric drive.
To be considered energy efficient a motors performance must equal or exceed the nominal full-load efficiency values provided by the National Electrical Manufacturers Association NEMA in publication MG 1. Brushless DC motors BLDC or permanent-magnet synchronous motors PMSM are pretty much the same thing and are the best to use as generators. Motor efficiency is the most important factor to consider in the development of implantable devices such as ventricular assist devices VADs and total artificial hearts TAHs.
The excess energy is dissipated as heat into the surrounding tissue and blood. Unlike most current EV motors the software-defined switched reluctance motors do not rely on permanent magnets or rare-earth minerals thus cutting costs and simplifying manufacturing. Generally an SCI motor is used for small appliances like say a bench saw.
For the majority of types of electrical motors you will likely use in your facilities you have a choice between AC or DC motor types. These two motor formats each have their own benefits and specific uses and sometimes the question of efficiency depends on which motor type you can choose based on its intended use. Thus a 10-horsepower hp motor has an acceptable load range of 5 to 10 hp.
A motor s efficiency tends to decrease dramatically below about 50 load. This eliminates the need for an efficiency. A cool 500000 savings and 86 tons of CO2 on just one motor.
The BLDC motors are the most preferred motors for the electric vehicle application due to its traction characteristics. Trade-offs like minimizing ohmic losses could cause increased iron losses. AC alternating current motors are used widely in industrial settings including common uses like pumps conveyors blowers and fans.
Over the lifetime of a motor the 025 higher efficiency can be very significant in terms of money and energy savings as well as profitability and environmental impact. It would also be really handy to give a rough price comparison of different power options as the most cost-effective motor that delivers the drive solution is generally sought. Regardless of motor type the described losses cannot be completely designed out.
There is no way to regulate the generated voltage except to regulate the speed. Electric motors can be powered by direct current DC sources such as from batteries motor vehicles. They generate AC so they require a rectifier on the output.
BLDC motors have traction characteristics like high starting torque high efficiency around 95-98 etc. The enclosure of the motor must protect the windings bearings and other mechanical parts from moisture chemicals mechanical damage and abrasion from grit. The design engineer needs to look at several possible designs in order to optimize the motor for the most efficient operation.
On the flip side the companys rotor is larger than those used in most electric cars which effectively gears the motor down for low rpm operation. Ongoing technical advancements continue to push the limits of how efficient these motors can be and the research and development underway in motor labs all over the world is yielding some really impressive results. Reasons to Determine Motor Loading Most electric motors are designed to run at 50 to 100 of rated load.
Specific full-load nominal efficiency values are provided for each horsepower hp enclosure type and speed combination. An electric motor is an electrical machine that converts electrical energy into mechanical energyMost electric motors operate through the interaction between the motors magnetic field and electric current in a wire winding to generate force in the form of torque applied on the motors shaft. Maximum efficiency is usually near 75 of rated load.
The electric energy that is input into the device is converted to mechanical energy by the motor. Peak efficiency is at 75 hp. NEMA standards MG1-125 through 127 define more than 20 types of enclosures under the categories of open machines totally enclosed machines and machines with encapsulated or sealed windings.
Right now is arguably the most exciting time in the nearly 200-year history of industrial electric motors. One little hydrogen fuel-cell vehicle holds the Guinness world record for the most efficient vehicle and uses a slotless brushless 60L-H-175-A from Koford Motors to drive its rear power wheel. Induction motor mainly uses electromagnetic induction for changing the energy from electric to mechanical.
This year the tiny car from the Duke Electric Vehicles team beat the 12600-mpg efficiency of the PAC CAR 2 in turn designed by a student team at the Eidgenoessische Technische Hochschule ETH in Zuerich Switzerland. A typical efficiency for this type of synchronous motor is approximately 982 to 988.
ads
Pages
Search This Blog
Blog Archive
- January 2023 (3)
- February 2022 (8)
- January 2022 (18)
- December 2021 (25)
- November 2021 (20)
- October 2021 (19)
- September 2021 (39)
- August 2021 (26)
- July 2021 (27)
- June 2021 (32)
- May 2021 (28)
- April 2021 (29)
- March 2021 (17)
- February 2021 (15)
- January 2021 (22)
- December 2020 (24)
- November 2020 (25)
- October 2020 (28)
- September 2020 (21)
- August 2020 (15)
- July 2020 (13)
- June 2020 (11)
- May 2020 (13)
- April 2020 (16)
- March 2020 (19)
- February 2020 (12)
- January 2020 (17)
- December 2019 (21)
- November 2019 (11)
- October 2019 (13)
- September 2019 (21)
- August 2019 (26)
- July 2019 (18)
- June 2019 (20)
- May 2019 (11)
Labels
- 12th
- 1920s
- 1939
- 1964
- 7q11
- abdominal
- abelard
- abiding
- ablative
- abnormal
- about
- abraham
- access
- accounting
- acid
- acne
- acquisitions
- acting
- action
- active
- activities
- activity
- actuators
- acuity
- acupuncture
- adaptation
- adaptive
- adhd
- adhesive
- adobe
- adults
- adventist
- affects
- africa
- after
- aids
- aircraft
- algernon
- algorithms
- alice
- alinski
- almond
- alpha
- america
- american
- amino
- amplifier
- amygdalin
- analysis
- anatomy
- andra
- andreas
- android
- anemia
- anesthesiologist
- aneurysm
- animals
- anova
- anterior
- anthology
- anti
- antibodies
- antietam
- antigen
- anxiety
- aortic
- apnea
- apple
- apraxia
- arduino
- areas
- aripiprazole
- army
- arrhythmogenic
- artery
- arthritis
- assessment
- assurance
- asthma
- atom
- atomic
- atresia
- atrial
- atypical
- audio
- augmentation
- augmented
- augustine
- autism
- autistic
- babies
- back
- backspin
- bacteria
- balance
- balm
- bariatric
- bark
- bartolome
- based
- battery
- battle
- beach
- beam
- behavior
- beings
- belief
- benefits
- benign
- best
- betta
- bifida
- bile
- biological
- biology
- bird
- birds
- bishop
- bismark
- black
- bleaching
- bleeding
- blocks
- blood
- blue
- board
- bonds
- bone
- book
- books
- borderline
- bowel
- boys
- bracelets
- brachial
- brain
- breast
- british
- brittle
- broom
- buddhism
- bugs
- building
- calcifications
- calculation
- calculator
- calculus
- california
- camera
- canaria
- canary
- cancer
- canyon
- capacitor
- capsule
- capsules
- carbide
- carbonate
- card
- care
- carnitine
- casco
- catheter
- catholic
- cattle
- cause
- causes
- cell
- cellulose
- cement
- central
- centrifuge
- ceramic
- chain
- chan
- change
- check
- chemotherapy
- chickering
- child
- childcare
- childhood
- children
- china
- chlamydia
- choice
- cholesterol
- chronic
- cinema
- ciprodex
- cirrhosis
- citizen
- city
- civil
- class
- classroom
- climate
- clinical
- clock
- clonic
- cloning
- cloud
- cluster
- coal
- coating
- code
- coefficient
- cognitive
- cold
- collaborate
- college
- coloboma
- colorado
- commerce
- common
- communication
- companies
- company
- compartment
- compensation
- complications
- composite
- compressed
- computer
- concepts
- condensing
- cone
- conflict
- conflicts
- conformation
- congestive
- connolly
- conquer
- conservation
- constipation
- construction
- consumer
- contact
- containers
- contaminated
- content
- contrast
- contribution
- control
- cooker
- cooled
- coral
- corporate
- correct
- corrosion
- cost
- counter
- counters
- country
- cpap
- cream
- creatine
- crime
- criminology
- crisis
- criteria
- cube
- culture
- curriculum
- cuts
- dahl
- dahmer
- daliresp
- damascus
- dark
- data
- date
- days
- death
- deaths
- debate
- decision
- defined
- definition
- degenerative
- dehydrogenase
- demand
- dense
- density
- dependence
- depression
- descriptive
- design
- designing
- desire
- desonide
- detention
- develop
- development
- device
- dexamethasone
- diabetes
- diagnosis
- diagnostic
- diagram
- dialogue
- dialysis
- diamond
- diarrhea
- dictionary
- dielectric
- digital
- dilation
- dina
- dioxide
- disabilities
- disability
- disc
- disease
- diseases
- disney
- disorder
- disorders
- dispensing
- diving
- document
- does
- dogs
- dollar
- donation
- doxycycline
- dragon
- dream
- dressing
- drilling
- drip
- driver
- drop
- drug
- drugs
- dryer
- duplication
- during
- dust
- duties
- dyslexia
- dysplasia
- earlobe
- early
- earth
- econometric
- economic
- economy
- edition
- education
- effects
- efficient
- effusion
- ehlers
- elasticity
- electric
- electricity
- electron
- electronic
- elmer
- embolism
- empire
- enbrel
- endometriosis
- endoscopy
- energy
- engineering
- england
- english
- enlarged
- environmental
- enzymes
- epidural
- epoxy
- epstein
- equality
- equations
- error
- ester
- ethics
- evaporation
- even
- evening
- evil
- exam
- examples
- excel
- exercise
- exercises
- existential
- expanding
- experiment
- explore
- extended
- extract
- facility
- factor
- factors
- facts
- failure
- fall
- family
- fatigue
- female
- fertilizer
- fibroid
- fibromyalgia
- field
- find
- fire
- fish
- fishing
- floating
- flow
- flowers
- fluid
- flying
- foam
- food
- foods
- footed
- foraminal
- forget
- formats
- fragile
- fraternal
- fray
- free
- french
- frequency
- from
- fuel
- function
- fundamentals
- fungicide
- futures
- gain
- gallbladder
- gauge
- gear
- gene
- genealogy
- generalized
- generators
- gift
- gilbert
- ginseng
- giving
- glandular
- glass
- gleevec
- glen
- global
- glutamic
- gluten
- golf
- good
- gorilla
- government
- grade
- grassland
- grassroots
- gravis
- green
- grid
- grind
- groin
- gross
- growth
- guide
- guidelines
- habitat
- hair
- handbook
- happiness
- have
- headache
- headaches
- health
- healthcare
- hearing
- heart
- heat
- hepatitis
- herbal
- herbs
- hernia
- high
- hinduism
- histone
- history
- hodgkin
- holder
- holes
- home
- honk
- hopi
- horizon
- hormone
- horn
- hour
- housing
- hubble
- human
- humans
- hydroponics
- hyper
- hyperkalemia
- idea
- identification
- identify
- identity
- illness
- illustrator
- imagination
- impact
- importance
- improvement
- income
- index
- indications
- indoor
- industry
- inequality
- infection
- informative
- injection
- injury
- insecticide
- insidious
- insipidus
- install
- insulin
- insurance
- intelligence
- intense
- interactive
- interesting
- international
- internet
- into
- intolerant
- intracranial
- introduction
- invasive
- invert
- involvement
- ipad
- iron
- irrigation
- islands
- isotopes
- issues
- italian
- itinerary
- james
- janet
- jeffrey
- jelly
- jellyfish
- jewish
- jobs
- john
- johnson
- joint
- judaism
- justice
- juva
- kansas
- karl
- kidney
- kids
- killer
- kinetic
- knock
- labels
- laboratory
- lack
- lactose
- ladder
- lamp
- language
- lantana
- laser
- last
- late
- latest
- lava
- leaf
- lean
- learning
- legal
- lemon
- lens
- leopard
- letters
- level
- levels
- lewy
- lids
- life
- lift
- light
- line
- lined
- lines
- lipoic
- liquid
- liquids
- list
- listen
- literature
- lithium
- liver
- locations
- long
- loss
- lower
- lumbar
- lumpectomy
- lung
- lyme
- lymph
- lymphoma
- lysosome
- lysosomes
- machine
- machines
- macht
- macular
- made
- maglev
- magnetic
- magnets
- major
- make
- maker
- making
- male
- managing
- manual
- maps
- maria
- maritime
- mark
- marker
- marx
- material
- materials
- mathematical
- maximum
- mean
- meaning
- mechanism
- media
- medical
- medication
- medications
- medicine
- meditation
- melanoma
- melbourne
- memory
- meningioma
- menopause
- mental
- mercury
- mergers
- mesenteric
- message
- methanol
- methods
- methotrexate
- michaels
- microbiome
- microencapsulated
- microscope
- middle
- migraine
- migratory
- mild
- mildew
- milk
- minecraft
- mining
- minnesota
- minocycline
- mite
- mitral
- model
- modeling
- models
- modern
- moisture
- money
- monitor
- monitoring
- monotheistic
- montessori
- mortise
- mosquitoes
- most
- motor
- mould
- mount
- mountain
- mousetrap
- muira
- municipal
- muscle
- muscles
- myasthenia
- mycorrhizal
- myelomeningocele
- mysterious
- name
- named
- narcolepsy
- narrative
- narwhals
- national
- natural
- nausea
- navy
- nebulizer
- neck
- neem
- negative
- network
- networking
- neural
- neuro
- newfoundland
- nicotine
- nietzsche
- night
- nile
- nitric
- nitrogen
- node
- nodules
- nonrenewable
- normal
- nose
- notes
- nuclear
- numbers
- nutrition
- obesity
- occlusion
- occur
- ocean
- officer
- olivia
- omega
- optometric
- oral
- order
- organ
- organisational
- osseous
- outage
- outlaw
- ovarian
- over
- overseas
- ovulation
- oxford
- pain
- painter
- palm
- pancreas
- panel
- panic
- pantheism
- papers
- papules
- parental
- particle
- patch
- patients
- peach
- pearly
- peel
- pelvic
- penile
- people
- performance
- pericardial
- period
- perkin
- personality
- perspectives
- phase
- philippines
- phosphate
- photography
- photos
- physical
- physically
- piaget
- pill
- pillows
- pills
- pine
- pipe
- pipes
- piston
- pituitary
- plans
- plant
- plastic
- plexus
- police
- pollutions
- poncirus
- pond
- pool
- poppers
- portland
- positioning
- positive
- possible
- post
- potassium
- pound
- powder
- power
- predestination
- pregnancy
- prenatal
- prentice
- preparation
- preschoolers
- presence
- pressure
- price
- prices
- primary
- prime
- primrose
- principles
- private
- problem
- produced
- proficiency
- profiling
- program
- programme
- properties
- prophets
- prostate
- prostitution
- protein
- psoriasis
- psychiatric
- psychotropic
- pubic
- public
- pulmonary
- pulsed
- pump
- pure
- puzzles
- pylori
- quadrant
- qualitative
- quality
- quantitative
- rack
- radiation
- radicals
- radioactive
- radiology
- radius
- rads
- ragweed
- rainforest
- rate
- ratio
- reactivity
- reactor
- reader
- reading
- reagan
- real
- reality
- reamer
- rebar
- recent
- recidivism
- recognize
- recordings
- rectal
- reduce
- refractive
- refrigeration
- regimens
- rehabilitation
- related
- relationships
- release
- relief
- religion
- remembrance
- removal
- renewable
- repair
- replacement
- reports
- republic
- research
- residents
- residual
- resolution
- resource
- response
- restoration
- results
- retinal
- review
- reviews
- rfid
- riboflavin
- rice
- rickets
- ridge
- right
- ring
- risk
- risks
- rituals
- river
- roald
- robins
- roman
- ronald
- rotc
- round
- saint
- saints
- sale
- salicylic
- saline
- salinity
- saliva
- salmon
- sample
- satellite
- saturated
- saul
- scale
- scan
- scanning
- scenarios
- scene
- schizoid
- science
- sciences
- score
- scotland
- security
- seed
- sense
- sensors
- separation
- series
- serious
- serum
- service
- services
- settings
- shakespeare
- shamed
- shell
- shipping
- short
- sickle
- side
- sign
- signaling
- signs
- sinus
- site
- skills
- sleep
- sleeping
- small
- smallest
- snow
- social
- society
- sociological
- software
- soil
- solar
- solution
- some
- something
- sonnets
- sort
- source
- space
- spanish
- speaking
- species
- spectrophotometer
- speed
- speller
- spill
- spina
- spinal
- spine
- sports
- squares
- squirrel
- stage
- stages
- stainless
- standards
- star
- starches
- state
- statistics
- status
- steel
- step
- stepper
- stepping
- stool
- stop
- storage
- stories
- stormwater
- stream
- strength
- subacute
- subq
- sufism
- sugar
- summary
- super
- supplements
- supply
- supra
- surgery
- survival
- survive
- switch
- sword
- sy5y
- symptoms
- syndrome
- system
- systems
- tags
- tailed
- talk
- tanker
- tanks
- tape
- target
- task
- tdap
- techniques
- technology
- teenage
- teens
- temperature
- tenon
- term
- terminal
- test
- testing
- testosterone
- tetanus
- text
- thailand
- themes
- theory
- therapy
- thermal
- thick
- things
- thinking
- thoracic
- threatened
- threatening
- thrips
- thyroid
- thyroiditis
- ties
- time
- titer
- tobacco
- tobramycin
- toddlers
- tomography
- tonic
- tool
- toolset
- touch
- toujeo
- trade
- traditional
- traffic
- train
- training
- transcendental
- transforma
- transplant
- trap
- treatment
- tree
- trees
- tribe
- tricuspid
- trifoliata
- triglycerides
- trisomy
- tube
- tudor
- tumor
- tunnel
- twain
- twins
- tyler
- type
- types
- tyre
- ultrapure
- unborn
- understanding
- unsaturated
- upper
- used
- uses
- usmle
- uterine
- vaccination
- vacuum
- valuable
- value
- values
- valve
- vatican
- vehicle
- vera
- verbal
- vero
- versailles
- versus
- vessels
- veterans
- vicar
- view
- village
- virtual
- virtue
- virus
- visual
- vitamin
- walk
- walt
- want
- warning
- watch
- water
- weather
- webroot
- weeks
- weight
- what
- wheel
- where
- which
- while
- white
- wiesbaden
- wild
- will
- wille
- willebrand
- windows
- wish
- with
- without
- wizard
- wolf
- women
- wood
- word
- words
- world
- wound
- writing
- wyoming
- yawn
- year
- your
- youth