So Lean is a philosophy and not a method of production or manufacturing. Lean service have among others been applied to US health care providers and the UK HMRC.
Lean In Manufacturing And Service Industry
Lean Thinking is by definition not product or industry specific in its principles and in its application even though its early roots were in the auto industry.
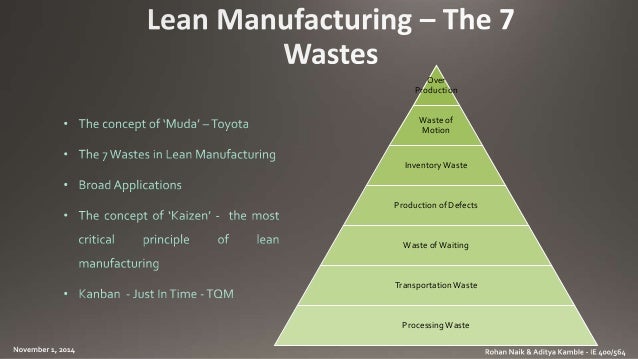
Lean in service industry. Lean service is an amalgamation of tools and practices which if applied appropriately would definitely improve the existing quality of operations and ensure the generation of a large amount of. It is as applicable in the service industry as it is in the auto industry. Lean can help to optimise all service delivery processes by targeting wastes and either removing them completely or move to a more effective state as part of a journey of continuous improvement.
It can be a manufacturing cell a service cell or a retail cell. It is about creating an agile engine which helps an organization weather the storm of competition. It is as applicable in the service industry as it is in the auto industry.
A small percentage of work typically eats up a disproportionate amount of time. It is about standardizing work processes to make problems visible and developing your team members critical thinking ability so that they can solve those problems and improve work processes. The above definition of the 8 wastes of Lean should be looked at as something that is directional and should always be kept in mind while taking up a Lean optimization project.
Companies in the service sector are constantly under pressure to deliver excellent customer service. So Lean is a philosophy and not a method of production or manufacturing. Lean Thinking is by definition not product or industry specific in its principles and in its application even though its early roots were in the auto industry.
Service context Service in this context is not limited to the office or administration but also wider service situations that are not necessarily repetitive where takt time is not applicable and where task times may be both long and variable. Lean in the Service Industry. Not all lean manufacturing ideas translate from factory floor to office cubicle.
In one internal support function 75 of transactions took less than five minutes to process. An IT company for example is very different from a manufacturing company however it still has many wasteful processes that could be removed or reduced. Piercy and Rich 2009.
Creating a lean culture Implementing lean services is really an exercise in change management. Teehan and Tucker 2010. Applying the Lean Principles in Service Industry.
Lean service is the application of lean manufacturing production methods tools and techniques in the service industry. These are also reported by service management or operations scholars Arbos 2002. For instance service workers are the best source of customer insight and suggestions for process improvements so its important to involve them in any lean initiative.
According to a study conducted by Cerioli 2009 the services sector has already demonstrated its relevance as an economic activity since classical Greece when young people received educationSubsequently other service activities were developed such as spices and textiles transportation through the silk route during the low Middle. History and evolution of lean production and services. The five Lean principles offer a basis for building an effective and productive organization.
Lets first define a work cell. Purpose This paper aims at highlighting the importance of Lean methodology through an exhaustive literature review and its implications and application in the Service industry right from its. Lean Training can help to optimise all service delivery processes by targeting wasteful processes and either removing them completely or move to a more effective state as part of a journey of continuous improvement.
Lean service is and how to lean service operations. Table 1 8 Wastes of Lean Manufacturing with Examples From Service Organizations. Leaning out a Service Industry F R A N K R Z E Z N I K I E W I C Z 2.
Interestingly there is a clear theoretical gap. A lean operating system alters the way a company learns through changes in problem solving coordination through connections and pathways and standardization. Lean gives administrators the ability to find inefficiencies in their company and provide more value to clients.
A typical observation within the service processes is a variation of the 80-20 rule. While all the principles hold true we need to understand that there are some specific details for Lean for service industry that might not be the same as Lean for the manufacturing industry. Lean Principles in the Service Industry.
Building a work cell can be confusing and difficult for someone with limited experience. The first principle of lean encourages us to understand value from the customer perspective but that activity is often based on the assumption that the product we are making is the right product. The idea of going to the gemba too is too often based on the assumption that we are producing what the customer wants.
Strategic Definition of Lean in a Service Context Lean is an improvement philosophy that targets to improve the performance of a business system by focusing on elements that do not add value. In Conclusion of the 8 Wastes of Lean Manufacturing. In terms of operations and improvements the service industries in general are a long way behind manufacturing.
Lean in the service industry 1. Dozens of success stories and white paper refer to cases with practical use of lean approaches in services. So the next time someone in your service organization tries to tell you that lean is just for manufacturing youll know better.
ads
Pages
Search This Blog
Blog Archive
- January 2023 (3)
- February 2022 (8)
- January 2022 (18)
- December 2021 (25)
- November 2021 (20)
- October 2021 (19)
- September 2021 (39)
- August 2021 (26)
- July 2021 (27)
- June 2021 (32)
- May 2021 (28)
- April 2021 (29)
- March 2021 (17)
- February 2021 (15)
- January 2021 (22)
- December 2020 (24)
- November 2020 (25)
- October 2020 (28)
- September 2020 (21)
- August 2020 (15)
- July 2020 (13)
- June 2020 (11)
- May 2020 (13)
- April 2020 (16)
- March 2020 (19)
- February 2020 (12)
- January 2020 (17)
- December 2019 (21)
- November 2019 (11)
- October 2019 (13)
- September 2019 (21)
- August 2019 (26)
- July 2019 (18)
- June 2019 (20)
- May 2019 (11)
Labels
- 12th
- 1920s
- 1939
- 1964
- 7q11
- abdominal
- abelard
- abiding
- ablative
- abnormal
- about
- abraham
- access
- accounting
- acid
- acne
- acquisitions
- acting
- action
- active
- activities
- activity
- actuators
- acuity
- acupuncture
- adaptation
- adaptive
- adhd
- adhesive
- adobe
- adults
- adventist
- affects
- africa
- after
- aids
- aircraft
- algernon
- algorithms
- alice
- alinski
- almond
- alpha
- america
- american
- amino
- amplifier
- amygdalin
- analysis
- anatomy
- andra
- andreas
- android
- anemia
- anesthesiologist
- aneurysm
- animals
- anova
- anterior
- anthology
- anti
- antibodies
- antietam
- antigen
- anxiety
- aortic
- apnea
- apple
- apraxia
- arduino
- areas
- aripiprazole
- army
- arrhythmogenic
- artery
- arthritis
- assessment
- assurance
- asthma
- atom
- atomic
- atresia
- atrial
- atypical
- audio
- augmentation
- augmented
- augustine
- autism
- autistic
- babies
- back
- backspin
- bacteria
- balance
- balm
- bariatric
- bark
- bartolome
- based
- battery
- battle
- beach
- beam
- behavior
- beings
- belief
- benefits
- benign
- best
- betta
- bifida
- bile
- biological
- biology
- bird
- birds
- bishop
- bismark
- black
- bleaching
- bleeding
- blocks
- blood
- blue
- board
- bonds
- bone
- book
- books
- borderline
- bowel
- boys
- bracelets
- brachial
- brain
- breast
- british
- brittle
- broom
- buddhism
- bugs
- building
- calcifications
- calculation
- calculator
- calculus
- california
- camera
- canaria
- canary
- cancer
- canyon
- capacitor
- capsule
- capsules
- carbide
- carbonate
- card
- care
- carnitine
- casco
- catheter
- catholic
- cattle
- cause
- causes
- cell
- cellulose
- cement
- central
- centrifuge
- ceramic
- chain
- chan
- change
- check
- chemotherapy
- chickering
- child
- childcare
- childhood
- children
- china
- chlamydia
- choice
- cholesterol
- chronic
- cinema
- ciprodex
- cirrhosis
- citizen
- city
- civil
- class
- classroom
- climate
- clinical
- clock
- clonic
- cloning
- cloud
- cluster
- coal
- coating
- code
- coefficient
- cognitive
- cold
- collaborate
- college
- coloboma
- colorado
- commerce
- common
- communication
- companies
- company
- compartment
- compensation
- complications
- composite
- compressed
- computer
- concepts
- condensing
- cone
- conflict
- conflicts
- conformation
- congestive
- connolly
- conquer
- conservation
- constipation
- construction
- consumer
- contact
- containers
- contaminated
- content
- contrast
- contribution
- control
- cooker
- cooled
- coral
- corporate
- correct
- corrosion
- cost
- counter
- counters
- country
- cpap
- cream
- creatine
- crime
- criminology
- crisis
- criteria
- cube
- culture
- curriculum
- cuts
- dahl
- dahmer
- daliresp
- damascus
- dark
- data
- date
- days
- death
- deaths
- debate
- decision
- defined
- definition
- degenerative
- dehydrogenase
- demand
- dense
- density
- dependence
- depression
- descriptive
- design
- designing
- desire
- desonide
- detention
- develop
- development
- device
- dexamethasone
- diabetes
- diagnosis
- diagnostic
- diagram
- dialogue
- dialysis
- diamond
- diarrhea
- dictionary
- dielectric
- digital
- dilation
- dina
- dioxide
- disabilities
- disability
- disc
- disease
- diseases
- disney
- disorder
- disorders
- dispensing
- diving
- document
- does
- dogs
- dollar
- donation
- doxycycline
- dragon
- dream
- dressing
- drilling
- drip
- driver
- drop
- drug
- drugs
- dryer
- duplication
- during
- dust
- duties
- dyslexia
- dysplasia
- earlobe
- early
- earth
- econometric
- economic
- economy
- edition
- education
- effects
- efficient
- effusion
- ehlers
- elasticity
- electric
- electricity
- electron
- electronic
- elmer
- embolism
- empire
- enbrel
- endometriosis
- endoscopy
- energy
- engineering
- england
- english
- enlarged
- environmental
- enzymes
- epidural
- epoxy
- epstein
- equality
- equations
- error
- ester
- ethics
- evaporation
- even
- evening
- evil
- exam
- examples
- excel
- exercise
- exercises
- existential
- expanding
- experiment
- explore
- extended
- extract
- facility
- factor
- factors
- facts
- failure
- fall
- family
- fatigue
- female
- fertilizer
- fibroid
- fibromyalgia
- field
- find
- fire
- fish
- fishing
- floating
- flow
- flowers
- fluid
- flying
- foam
- food
- foods
- footed
- foraminal
- forget
- formats
- fragile
- fraternal
- fray
- free
- french
- frequency
- from
- fuel
- function
- fundamentals
- fungicide
- futures
- gain
- gallbladder
- gauge
- gear
- gene
- genealogy
- generalized
- generators
- gift
- gilbert
- ginseng
- giving
- glandular
- glass
- gleevec
- glen
- global
- glutamic
- gluten
- golf
- good
- gorilla
- government
- grade
- grassland
- grassroots
- gravis
- green
- grid
- grind
- groin
- gross
- growth
- guide
- guidelines
- habitat
- hair
- handbook
- happiness
- have
- headache
- headaches
- health
- healthcare
- hearing
- heart
- heat
- hepatitis
- herbal
- herbs
- hernia
- high
- hinduism
- histone
- history
- hodgkin
- holder
- holes
- home
- honk
- hopi
- horizon
- hormone
- horn
- hour
- housing
- hubble
- human
- humans
- hydroponics
- hyper
- hyperkalemia
- idea
- identification
- identify
- identity
- illness
- illustrator
- imagination
- impact
- importance
- improvement
- income
- index
- indications
- indoor
- industry
- inequality
- infection
- informative
- injection
- injury
- insecticide
- insidious
- insipidus
- install
- insulin
- insurance
- intelligence
- intense
- interactive
- interesting
- international
- internet
- into
- intolerant
- intracranial
- introduction
- invasive
- invert
- involvement
- ipad
- iron
- irrigation
- islands
- isotopes
- issues
- italian
- itinerary
- james
- janet
- jeffrey
- jelly
- jellyfish
- jewish
- jobs
- john
- johnson
- joint
- judaism
- justice
- juva
- kansas
- karl
- kidney
- kids
- killer
- kinetic
- knock
- labels
- laboratory
- lack
- lactose
- ladder
- lamp
- language
- lantana
- laser
- last
- late
- latest
- lava
- leaf
- lean
- learning
- legal
- lemon
- lens
- leopard
- letters
- level
- levels
- lewy
- lids
- life
- lift
- light
- line
- lined
- lines
- lipoic
- liquid
- liquids
- list
- listen
- literature
- lithium
- liver
- locations
- long
- loss
- lower
- lumbar
- lumpectomy
- lung
- lyme
- lymph
- lymphoma
- lysosome
- lysosomes
- machine
- machines
- macht
- macular
- made
- maglev
- magnetic
- magnets
- major
- make
- maker
- making
- male
- managing
- manual
- maps
- maria
- maritime
- mark
- marker
- marx
- material
- materials
- mathematical
- maximum
- mean
- meaning
- mechanism
- media
- medical
- medication
- medications
- medicine
- meditation
- melanoma
- melbourne
- memory
- meningioma
- menopause
- mental
- mercury
- mergers
- mesenteric
- message
- methanol
- methods
- methotrexate
- michaels
- microbiome
- microencapsulated
- microscope
- middle
- migraine
- migratory
- mild
- mildew
- milk
- minecraft
- mining
- minnesota
- minocycline
- mite
- mitral
- model
- modeling
- models
- modern
- moisture
- money
- monitor
- monitoring
- monotheistic
- montessori
- mortise
- mosquitoes
- most
- motor
- mould
- mount
- mountain
- mousetrap
- muira
- municipal
- muscle
- muscles
- myasthenia
- mycorrhizal
- myelomeningocele
- mysterious
- name
- named
- narcolepsy
- narrative
- narwhals
- national
- natural
- nausea
- navy
- nebulizer
- neck
- neem
- negative
- network
- networking
- neural
- neuro
- newfoundland
- nicotine
- nietzsche
- night
- nile
- nitric
- nitrogen
- node
- nodules
- nonrenewable
- normal
- nose
- notes
- nuclear
- numbers
- nutrition
- obesity
- occlusion
- occur
- ocean
- officer
- olivia
- omega
- optometric
- oral
- order
- organ
- organisational
- osseous
- outage
- outlaw
- ovarian
- over
- overseas
- ovulation
- oxford
- pain
- painter
- palm
- pancreas
- panel
- panic
- pantheism
- papers
- papules
- parental
- particle
- patch
- patients
- peach
- pearly
- peel
- pelvic
- penile
- people
- performance
- pericardial
- period
- perkin
- personality
- perspectives
- phase
- philippines
- phosphate
- photography
- photos
- physical
- physically
- piaget
- pill
- pillows
- pills
- pine
- pipe
- pipes
- piston
- pituitary
- plans
- plant
- plastic
- plexus
- police
- pollutions
- poncirus
- pond
- pool
- poppers
- portland
- positioning
- positive
- possible
- post
- potassium
- pound
- powder
- power
- predestination
- pregnancy
- prenatal
- prentice
- preparation
- preschoolers
- presence
- pressure
- price
- prices
- primary
- prime
- primrose
- principles
- private
- problem
- produced
- proficiency
- profiling
- program
- programme
- properties
- prophets
- prostate
- prostitution
- protein
- psoriasis
- psychiatric
- psychotropic
- pubic
- public
- pulmonary
- pulsed
- pump
- pure
- puzzles
- pylori
- quadrant
- qualitative
- quality
- quantitative
- rack
- radiation
- radicals
- radioactive
- radiology
- radius
- rads
- ragweed
- rainforest
- rate
- ratio
- reactivity
- reactor
- reader
- reading
- reagan
- real
- reality
- reamer
- rebar
- recent
- recidivism
- recognize
- recordings
- rectal
- reduce
- refractive
- refrigeration
- regimens
- rehabilitation
- related
- relationships
- release
- relief
- religion
- remembrance
- removal
- renewable
- repair
- replacement
- reports
- republic
- research
- residents
- residual
- resolution
- resource
- response
- restoration
- results
- retinal
- review
- reviews
- rfid
- riboflavin
- rice
- rickets
- ridge
- right
- ring
- risk
- risks
- rituals
- river
- roald
- robins
- roman
- ronald
- rotc
- round
- saint
- saints
- sale
- salicylic
- saline
- salinity
- saliva
- salmon
- sample
- satellite
- saturated
- saul
- scale
- scan
- scanning
- scenarios
- scene
- schizoid
- science
- sciences
- score
- scotland
- security
- seed
- sense
- sensors
- separation
- series
- serious
- serum
- service
- services
- settings
- shakespeare
- shamed
- shell
- shipping
- short
- sickle
- side
- sign
- signaling
- signs
- sinus
- site
- skills
- sleep
- sleeping
- small
- smallest
- snow
- social
- society
- sociological
- software
- soil
- solar
- solution
- some
- something
- sonnets
- sort
- source
- space
- spanish
- speaking
- species
- spectrophotometer
- speed
- speller
- spill
- spina
- spinal
- spine
- sports
- squares
- squirrel
- stage
- stages
- stainless
- standards
- star
- starches
- state
- statistics
- status
- steel
- step
- stepper
- stepping
- stool
- stop
- storage
- stories
- stormwater
- stream
- strength
- subacute
- subq
- sufism
- sugar
- summary
- super
- supplements
- supply
- supra
- surgery
- survival
- survive
- switch
- sword
- sy5y
- symptoms
- syndrome
- system
- systems
- tags
- tailed
- talk
- tanker
- tanks
- tape
- target
- task
- tdap
- techniques
- technology
- teenage
- teens
- temperature
- tenon
- term
- terminal
- test
- testing
- testosterone
- tetanus
- text
- thailand
- themes
- theory
- therapy
- thermal
- thick
- things
- thinking
- thoracic
- threatened
- threatening
- thrips
- thyroid
- thyroiditis
- ties
- time
- titer
- tobacco
- tobramycin
- toddlers
- tomography
- tonic
- tool
- toolset
- touch
- toujeo
- trade
- traditional
- traffic
- train
- training
- transcendental
- transforma
- transplant
- trap
- treatment
- tree
- trees
- tribe
- tricuspid
- trifoliata
- triglycerides
- trisomy
- tube
- tudor
- tumor
- tunnel
- twain
- twins
- tyler
- type
- types
- tyre
- ultrapure
- unborn
- understanding
- unsaturated
- upper
- used
- uses
- usmle
- uterine
- vaccination
- vacuum
- valuable
- value
- values
- valve
- vatican
- vehicle
- vera
- verbal
- vero
- versailles
- versus
- vessels
- veterans
- vicar
- view
- village
- virtual
- virtue
- virus
- visual
- vitamin
- walk
- walt
- want
- warning
- watch
- water
- weather
- webroot
- weeks
- weight
- what
- wheel
- where
- which
- while
- white
- wiesbaden
- wild
- will
- wille
- willebrand
- windows
- wish
- with
- without
- wizard
- wolf
- women
- wood
- word
- words
- world
- wound
- writing
- wyoming
- yawn
- year
- your
- youth